Document details
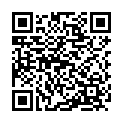
Abstract
The exponential increase in the number of manmade objects in Earth orbits has to be smartly managed, if we do not want to imprison ourselves in our planet in the near future. Every month several dozen new satellites are launched, which contributes eventually to the total amount space debris. “Design-for-Demise” or “D4D” approach means that the satellites must disintegrate during an uncontrolled atmospheric entry and the fragments should burn down to a level where there is no substantial risk posed on ground for life or property. At German Aerospace Center (DLR) Institute of Structures and Design in Stuttgart, we have been developing high-altitude break-up concepts since 2020 [ref]. The objective is to trigger the primary structure break-up at much higher altitudes than they naturally would disintegrate, so that the inner components, which are known to be critical to demise, have longer exposure time to high temperature plasma flows for an enhanced demise behaviour.
DLR Institute of Structures and Design (BT) is heavily involved with sustainability in space from demisable satellite structures all the way to the replacement of state-if-the-art with more sustainable material alternatives for both better demise behaviour and less environmental impact on the atmosphere during their re-entry. DLR-BT also has a long-time experience in advanced manufacturing techniques for aircraft and spacecraft, in addition to advanced materials that are used for high temperature applications of atmospheric entry. The “Integrated Platform for Affordable Satellites” (IRAS) Project [ref] is a specific instance of such activities, where advanced additive manufacturing techniques for printed thermoplastics, ceramics and metals were investigated for topology optimized, bionic and multifunctional sandwich structures for satellite applications.
Using the experience and competences from IRAS and many other ESA and EU projects, we have developed hybrid and additively manufactured demisable joints, that have the mechanical and thermal strength to endure the launch and orbital loads, but would allow for a high-altitude break-up for both small satellites of order ~100 kg as well as large satellites of >1000 kg. In this study, a 3D printed hybrid joint reinforced by a passive ejection mechanism based on SMA and compression springs will be presented. Our test case was based on Sentinel-6 satellite. The fragmentation simulations were performed by HTG’s SCARAB tool. Different scenarios were analysed to optimize the disintegration sequences by replacing regular joints with demisable ones at selected locations. The break-up altitudes could be improved from 97 km to 115 km and the debris casualty area could be reduced by 60%.
Preview

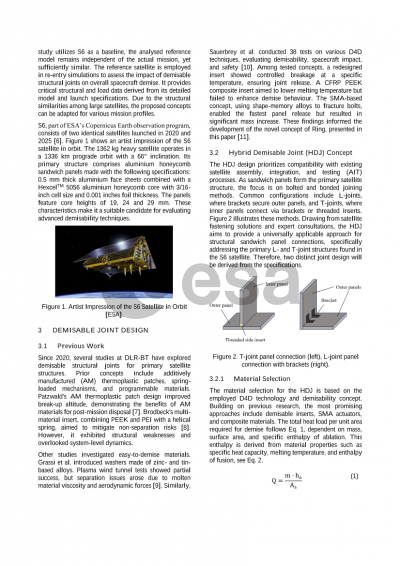
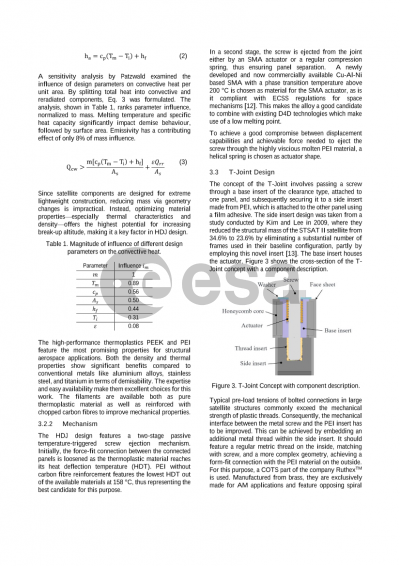
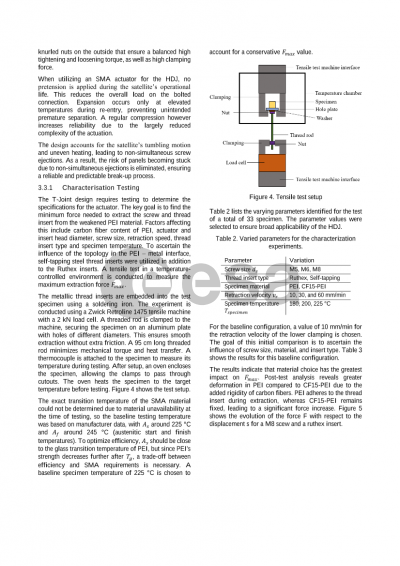
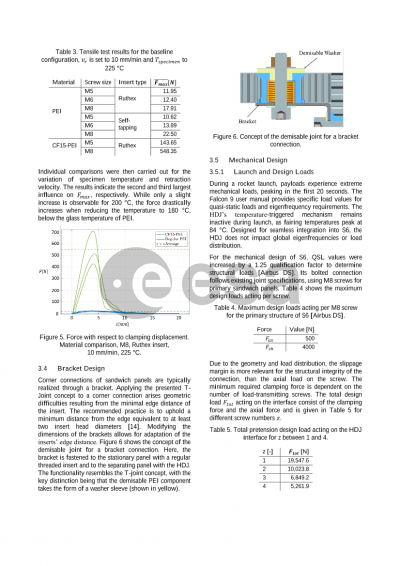
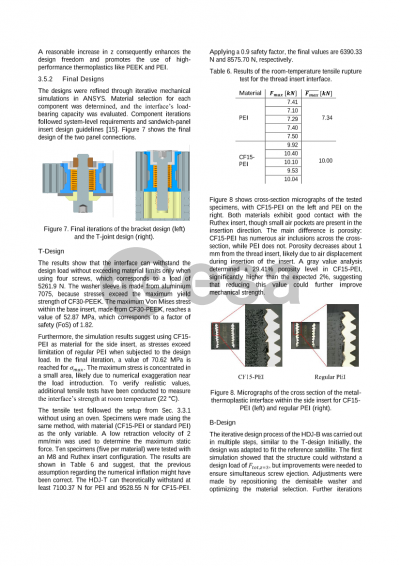
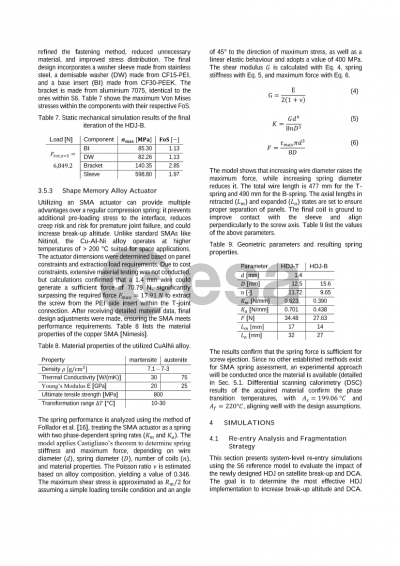
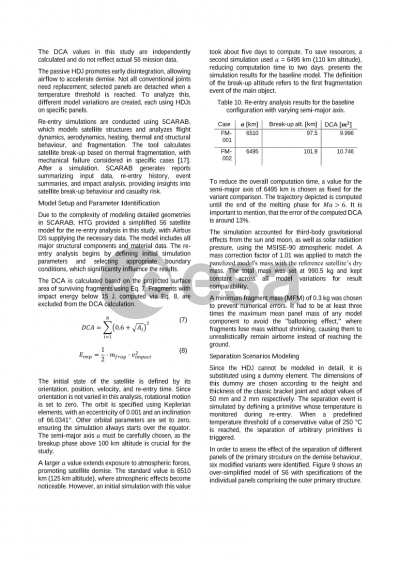
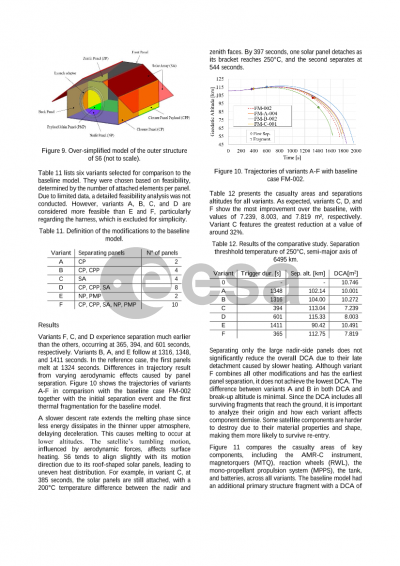
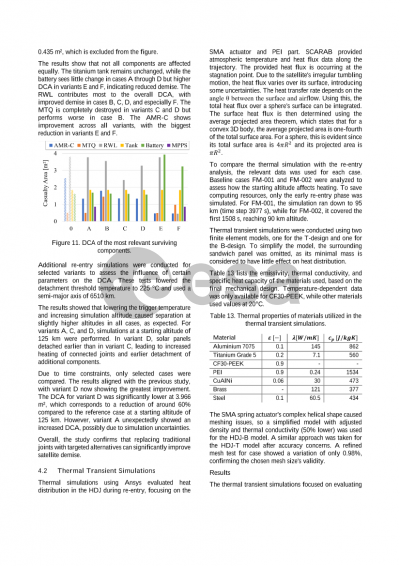
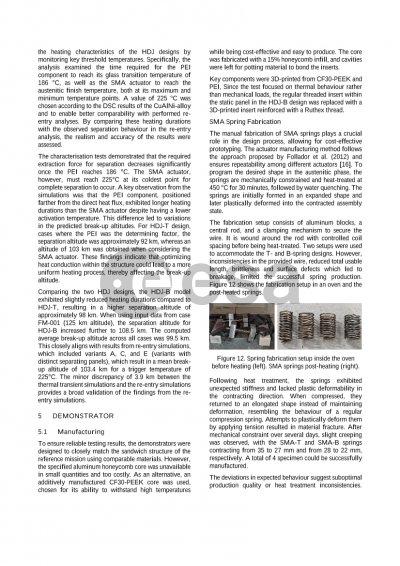
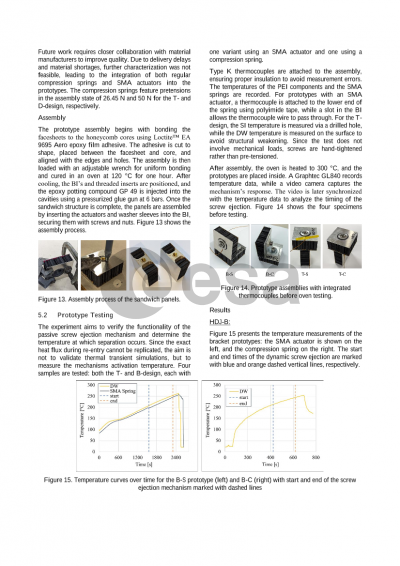
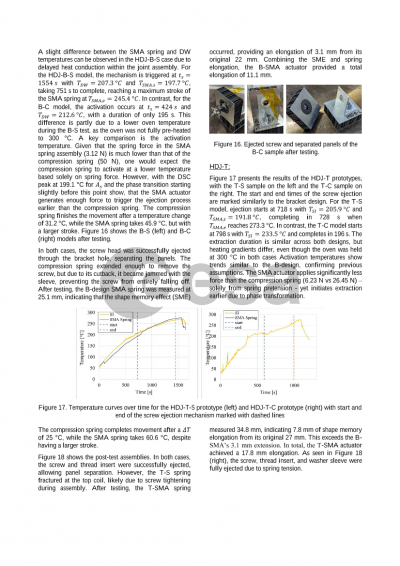
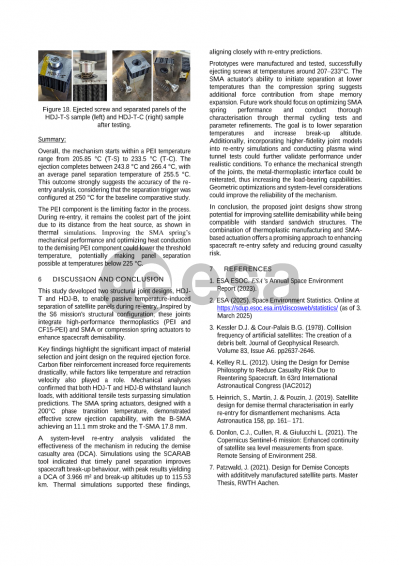
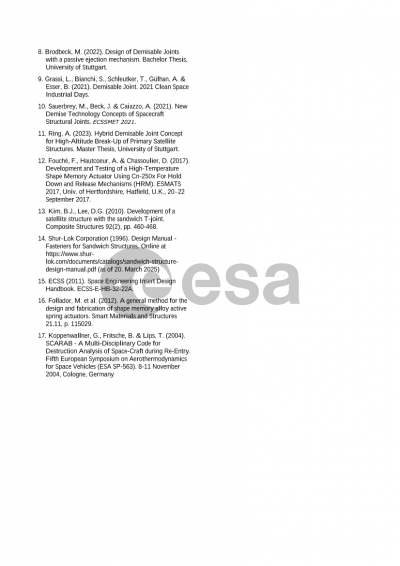
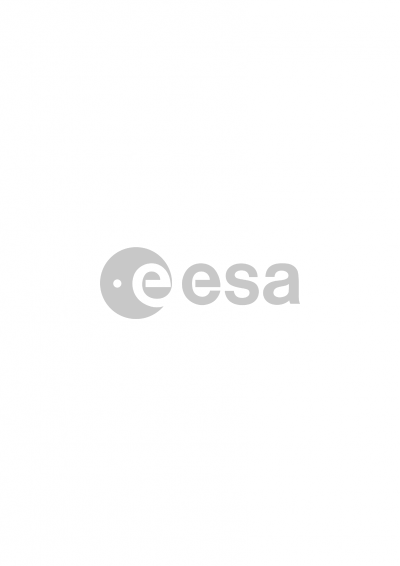