Document details
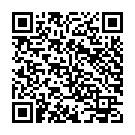
Abstract
With the increasing presence of orbital debris, Design for Demise (D4D) has become essential to ensure safe and sustainable space operations. D4D aims to minimise the risk of human casualty on Earth by ensuring that satellite components fully disintegrate during re-entry, preventing debris from reaching the ground. As part of the European Space Agency’s (ESA) Zero Debris approach, this paper presents the results obtained in D4D research including materials (glasses and composites), and critical components for the casualty risk (electronics, bipods and thrusters). Moreover, this paper provides an overview of lessons learned from these studies, contributing to develop a robust understanding of demise behaviour improving spacecraft design.
The paper presents D4D advancements in material studies, particularly focusing on Fused Silica, Zerodur, Carbon Fibre-Reinforced Polymer (CFRP) and Flax Fibre Reinforced Polymer (FFRP). A model for glass material demise has been developed, showing that disintegration rates are closely related to material viscosity and surface temperature. Additionally, studies into composites highlight that the choice of fibre materials and joint configuration can significantly impact demisability. Research has demonstrated the potential for improved demise when incorporating discontinuous and flax fibres, laying the foundations for D4D composite structures balancing performance with demisability.
In addition, the paper presents research performed in the demise of satellite components, specifically electronics, thrusters and bipods. For electronics, studies highlight the influence of component configuration and material choice on demisability. Research on thrusters shows that subcomponents such as inlets and nozzles demise differently based on material composition, structural configuration, and dynamic forces, with the lower section typically demising faster than the upper. Findings highlight the importance of accounting for shock-induced failures and thermal dynamics in models, especially for complex alloys like Haynes 25, which have shown greater re-entry resilience than anticipated. Finally, bipod designs were characterised, and demisable bipods were designed using additive manufacturing to create hollow structures with integrated holes, enhancing demisability by increasing locally the heat flux through flow holes.
In parallel, ESA’s Zero Debris Platforms initiatives are underway, working with industry to create the next generation of satellite platforms (across large and small satellites and CubeSats) fully compliant with the Space Debris Mitigation standards to achieve Zero Debris satellite platforms by 2030. By adapting D4D design solutions in the platform design, ESA aims to ensure that platform meet the technological needs for space sustainability. Through this approach, ESA is establishing a new benchmark in D4D and advancing solutions for a safer orbital environment.
Preview
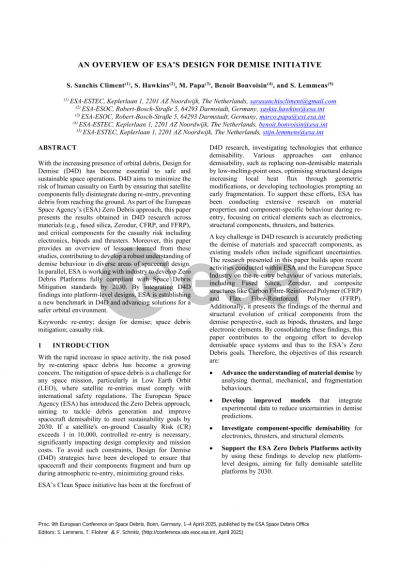
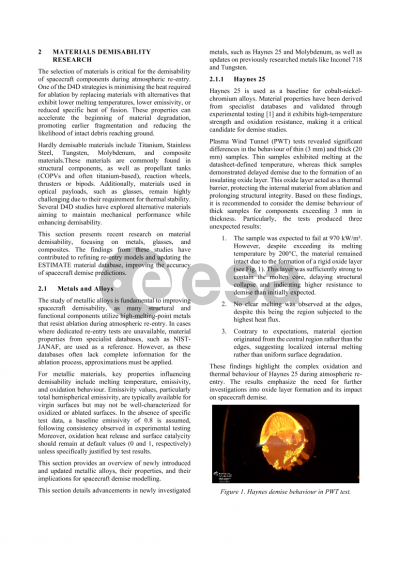
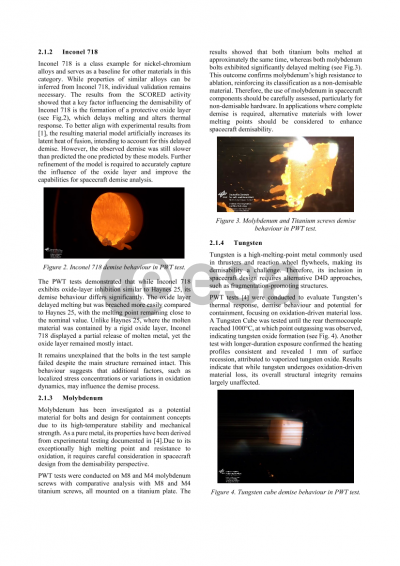
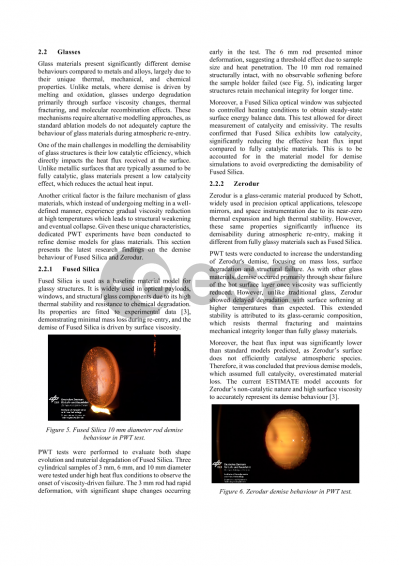
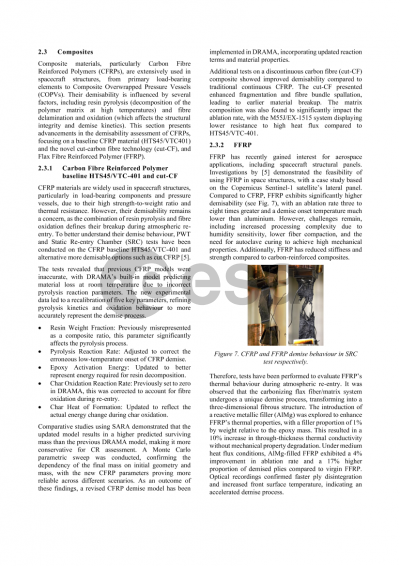
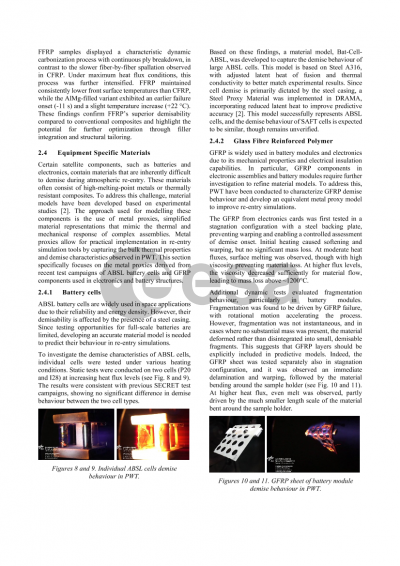

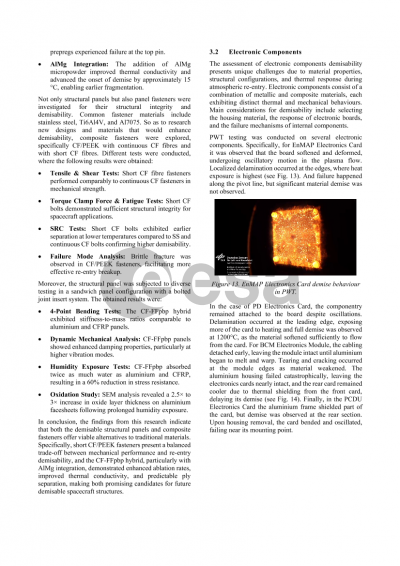
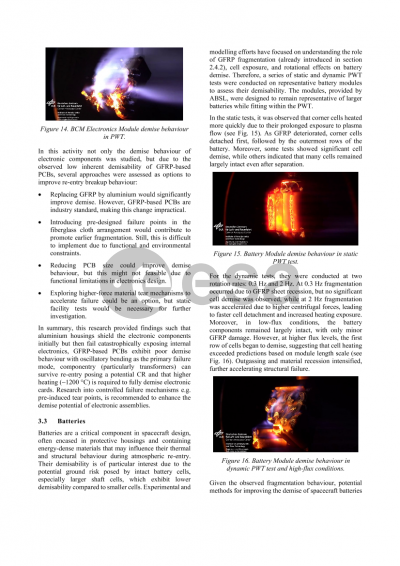
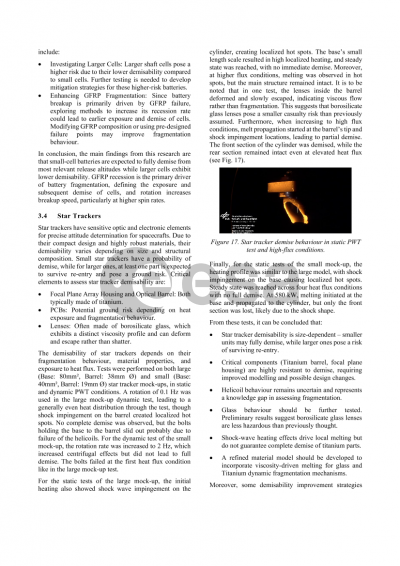
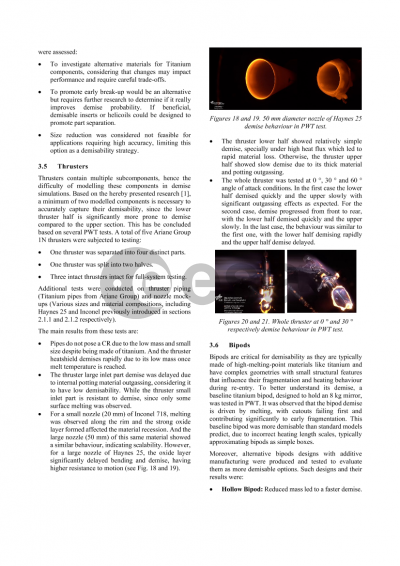
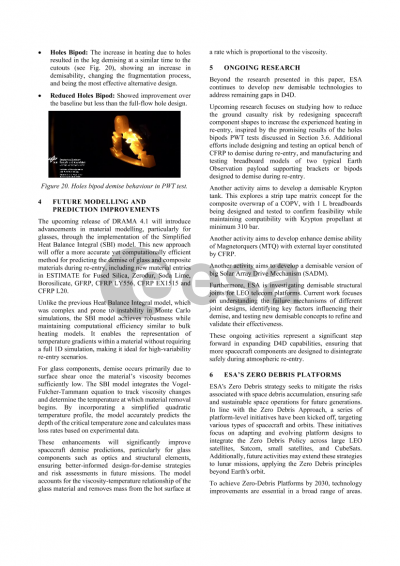
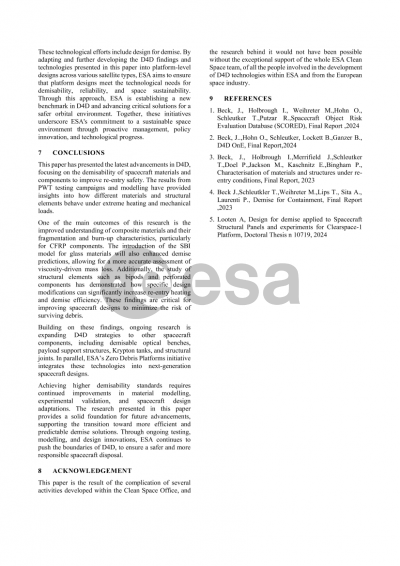