Document details
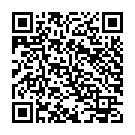
Abstract
We will consider the case of a satellite hydrazine fuel tank and the consequences of a hyper-velocity impact from space debris. The final purpose of this study is to better understand the mechanisms of detonation of hydrazine vapor during a hypervelocity impact on a low-pressure reservoir.
In the ratio of hoop stress to fracture stress vs. crushing limit energy described in ISO16126, the explanation is that the operation starts at a stress ratio of 0.5 and does not fracture from about 0.25. Understand the fracturing conditions of propellant tanks for satellites and protect against debris that could lead to total loss of satellites.
Obtain basic data on the guidelines for protective design. In the process, a circular tank that simulates an actual tank is prototyped, and the experimental correlation equation presented in ISO for tank fracturing is evaluated and compared, and the presence or absence of crushing due to the difference between pressurized and non-pressurized is confirmed. As part of this effort, The response to a hiper velocity impact of 7 km/s under pressurized and unpressurized Ti-6Al-4V plates used in tank materials is shown and discussed.
We confirmed the sabot function at the maximum energy that can be performed with the ISAS-JAXA two-stage light gas gun.
A high-speed impact test of 7 km/sec was conducted using the injection of a polycarbonate sphere Φ7.18 mm, which can achieve the maximum energy conditions.
A specimen chamber was made in the shape of two circular plates sandwiched together, and the internal pressure was varied from no pressure to 1 MPa to verify whether the appearance of penetration, fracturing, etc. during impact would differ depending on the internal pressure. The impact velocity was also varied from 5 to 7 km/sec to verify whether the appearance of impact would differ depending on the impact energy. Under the condition that the thickness of the tita-nium plate on the impact surface was 0.62 mm, only penetration occurred without pressuriza-tion, and two bumps and cracks occurred in the direction of the impact surface at 0.6 Mpa. Fur-thermore, when the pressurization was 1.09 Mp, fracturing occurred from the penetrating por-tion and half of the fragments were separated.
As a result, it was found that the difference in the internal pressure of the test specimen at least caused a difference in penetration and fracturing. We will continue to examine the effects of pressure and the energy conditions that cause fracturing, and we plan to conduct verification using test specimens equivalent to the tanks actually used in orbit.
Preview
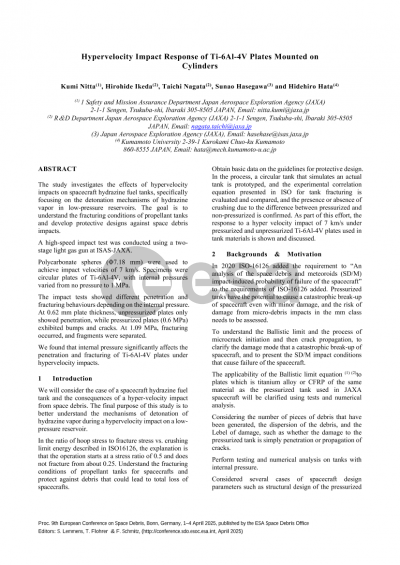
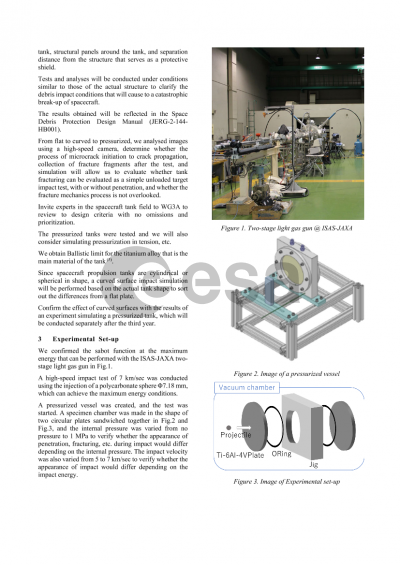

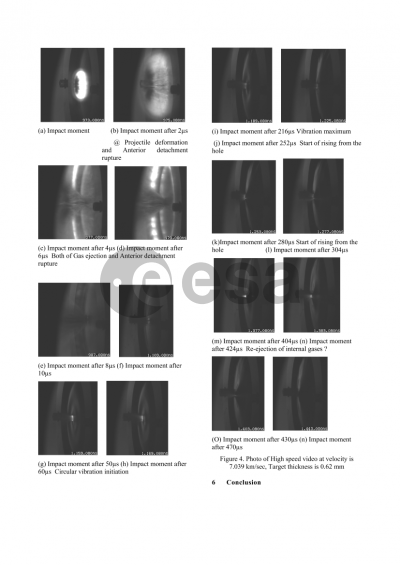
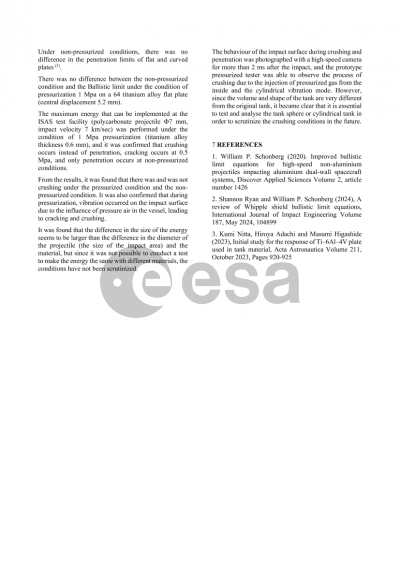