Document details
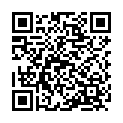
Abstract
Additive manufacturing (AM) is becoming widely used across many industrial sectors, which is pushing the capabilities of the printers and processes. As a result, Design for Additive Manufacturing (DFAM) is becoming more prevalent and the technology is making its way into the space industry. For satellite design, AM has the potential to reduce weight, volume and cost of satellites with a positive impact on the payload mass ratio and space accessibility. More specifically, satellite
orbital debris shields, which are currently produced using conventional manufacturing techniques, and are limited in terms of design variation, can benefit greatly from the flexibility offered by 3D printing.
Through the use of Additive Manufacturing one can easily produce, test and integrate a wider range of shield designs. This can lead to having more optimized orbital debris shields for specific applications which will result in a better protection for the spacecraft. At the same time, since the shields are printed out of solid materials, they can augment and support the primary structure of the satellite in its load bearing functions.
The objective of this paper is to present a structural assessment of AlSi10Mg 3D printed corrugated orbital debris shields. This assessment is carried out using experimental data generated from 18 static structural samples and 21 hypervelocity impact (HVI) samples manufactured and tested as part of the EU funded ReDSHIFT project. The samples were subjected to three point bending, compression and HVI - the three loading scenarios relevant for both structural and shielding purposes. Experimental results are compared to the performance of CFRP sandwich panels with a 3D printed honeycomb core as well as a standard honeycomb core. The comparison gives insight into the structural value of the proposed novel shields. Finally, the experimental results
are compared to Finite Element Analysis (FEA) carried out within the ANSYS APDL 2020 environment (bending and compression) and in AUTODYN (HVI). The use of relevant theory is made to interpret and explain the results, where possible. Material models for printed AlSi10Mg
are validated and can be used in the development of such novel corrugated shields that have the potential of playing a structural role in the future.
Preview

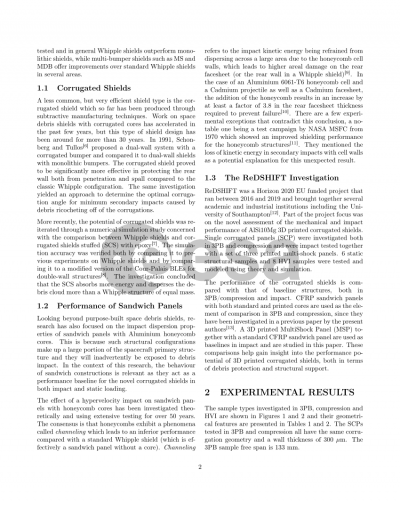


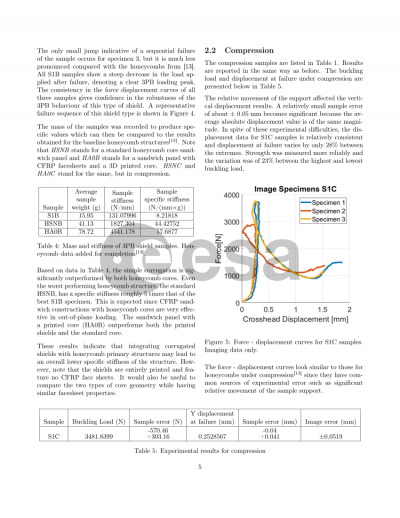

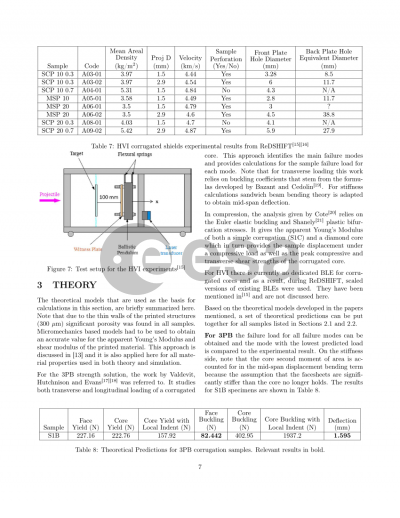


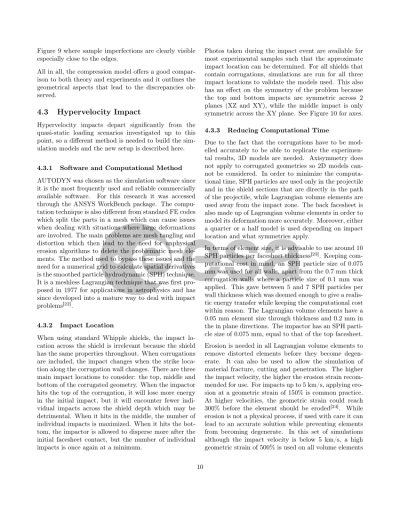

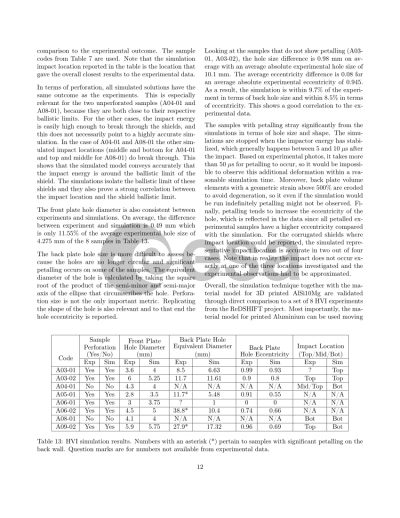
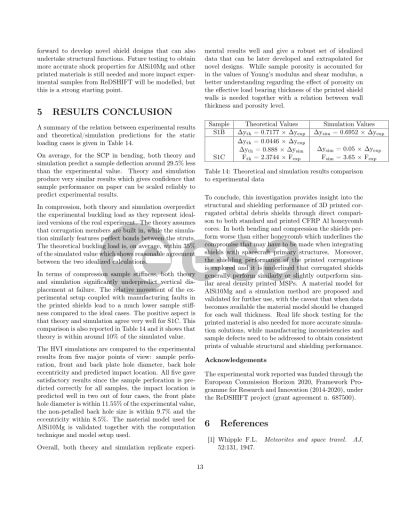

