Document details
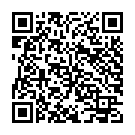
Abstract
The continuous research in the micro-meteoroid and orbital debris (MMOD) shield design has embraced the need for weight saving and structurally effective shields. The multi-purpose sandwich structures with foam core have been studied to compensate for the shortcoming of other single-purpose shield designs by eliminating the need for the imposition of parasitic components and by offering an excellent combination of structural, thermal and energy absorption properties.
The geometry of the real aluminum foam is a complex 3D lattice structure with an enormous number of tiny individual members when compared to the overall dimensions of the panel, which represents a significant challenge for the simulation. In this study, statistical information obtained from the physical foam was used to develop an efficient numerical foam model. The translational unit (TU) of the Wearie-Phelan idealization was scaled to achieve the target pores per inch (PPI) parameter based on the selected average ligament size. The developed TU was used as building blocks to form a 3D bubble structure. A randomization algorithm was applied for the obtained wireframe, moving each node in a random direction by a small random value. Spheres of a given constant diameter were created at the nodes of the wireframe, and cylinders were created to represent the ligaments. The resulting solid body was cut to the desired dimensions of the specimen selected for the numerical impact testing.
The projectile, front face sheet and foam core were modelled using the SPH approach, while the rear face sheet was meshed with finite elements. This highly detailed numerical model was applied to conduct the numerical impact tests of a 6-mm spherical aluminum particle at 7 km/s on the aluminum foam core sandwich panels and validated via comparison with experimental data. The obtained model provides the visualization of the propagation of debris within the panel structure, allowing to use it as a tool for understanding the dominating physical mechanisms of perforation and ways to provide improvement of shielding efficiency of the panel.
Preview
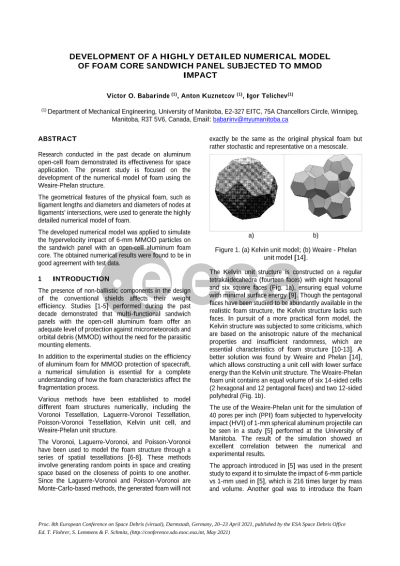

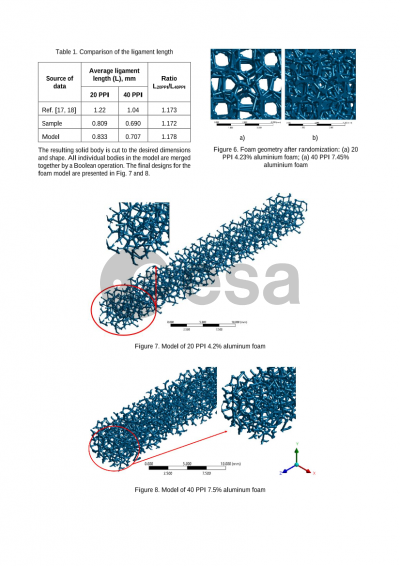
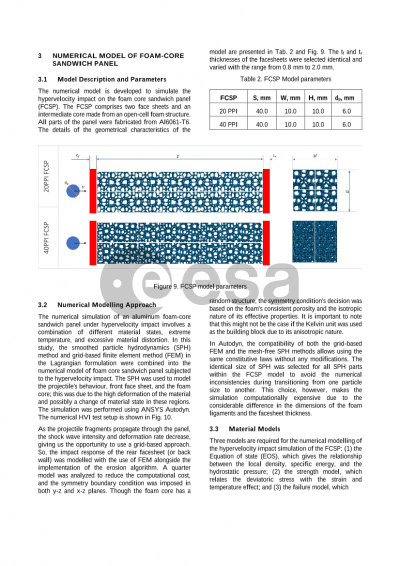

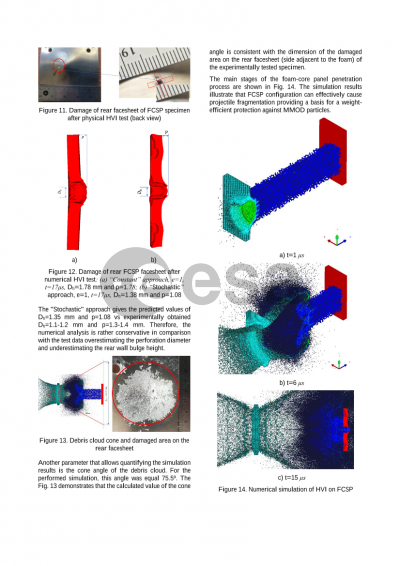
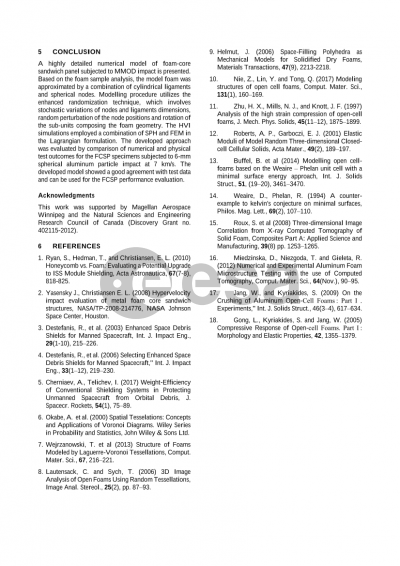