Document details
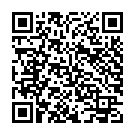
Abstract
The behavior of composite materials, specifically carbon fiber reinforced plastic (CFRP) and glass fiber reinforced plastic (GFRP), under reentry conditions poses a problem for space debris reentry risk modeling. Since these materials pyrolyze rather than melt and their different components demise at different rates, modeling their destruction to determine ground impact risk is complex. Modern spacecraft are using these materials in ever-greater quantities owing to their superior strength-to-weight characteristics, and this has required that the orbital debris community improve its understanding of how these materials demise on reentry.
The NASA Orbital Debris Program Office undertook an extensive test campaign to better understand the rate at which several types of GFRP and CFRP materials pyrolyze under reentry heating conditions and how that pyrolysis affects their ultimate strength. GFRP with a polyester resin (G10/FR-4) and CFRP with epoxy, cyanate ester, vinyl ester, and phenolic resins were tested. The test campaign was carried out at the Inductively Coupled Plasma (ICP) Torch Facility at the University of Texas at Austin. Because the ICP facility operates in a shirt-sleeve environment, test samples can be changed within seconds or minutes, allowing many samples to be tested in a short period. Two heat flux rates, 20 W/m2 and 30 W/m2, and two oxygen concentration conditions, 0% and 2% of atmospheric, were applied to all five types of material. To measure both the char rate and the effect of pyrolysis on the ultimate strength of the material, two types of test were carried out for each material: a char rate test on a ~10 mm thick sample of material and an in-situ bending stress test of a ~2 mm thick sample of material.
Measurements of the char rate showed very similar average pyrolysis front velocity in epoxy resin CFRP as in G10 at 3.6 mm/min and 3.4 mm/min, respectively. However, the total mass loss rate in the G10 was nearly double that of the CFRP at 3.8 g/min and 2.2 g/min, respectively. This result represented a slow ablation rate of carbon fibers in the CFRP at the temperatures encountered in low Earth orbit reentry and a comparatively rapid removal of the glass fibers in G10 due to melting and spallation. Pyrolysis front velocity was more significantly affected by the type of plastic than the type of fiber, with the cyanate ester CFRP samples displaying an average pyrolysis front velocity of only 1.9 mm/min.
Similarly, the effect of thermal exposure on the ultimate strength of the material depended heavily on the type of plastic and very little on the type of fiber in the material. Epoxy, vinyl ester, and polyester resins all behaved very similarly, with complete structural failure at between 400 J/g and 600 J/g of specific absorbed heat. Phenolic and cyanate ester resins, on the other hand, displayed a change in structural properties that was only barely measurable with the current apparatus even after the maximum exposure time tested.
These data are being incorporated into a numerical model of the ablation and demise of composite materials that will be used to more accurately calculate the ground casualty risk of future spacecraft.
Preview
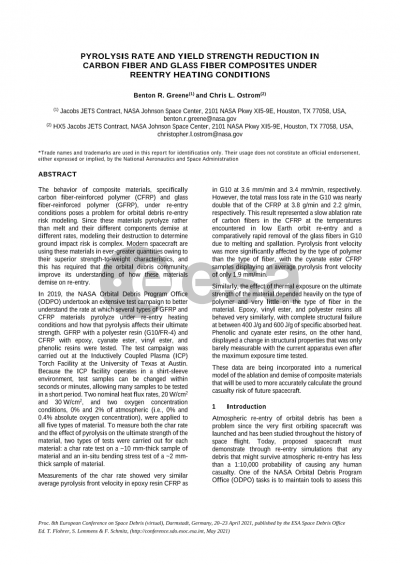
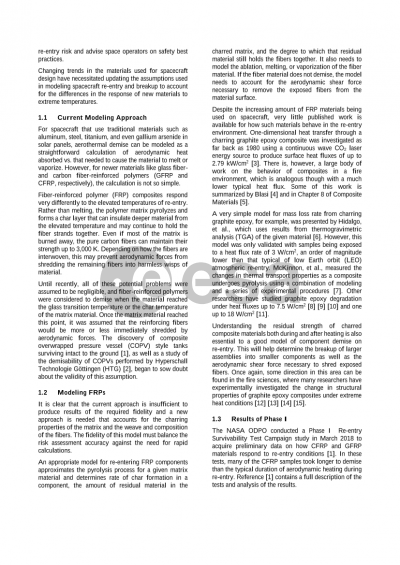


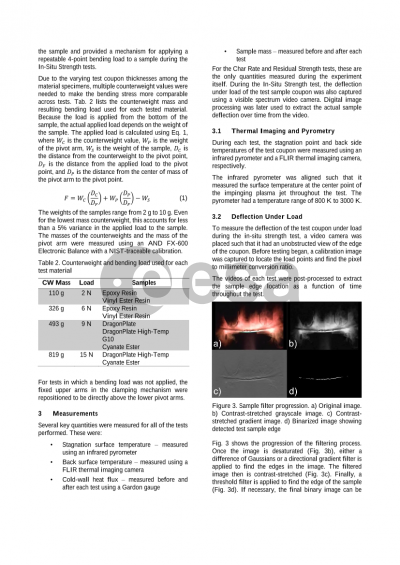

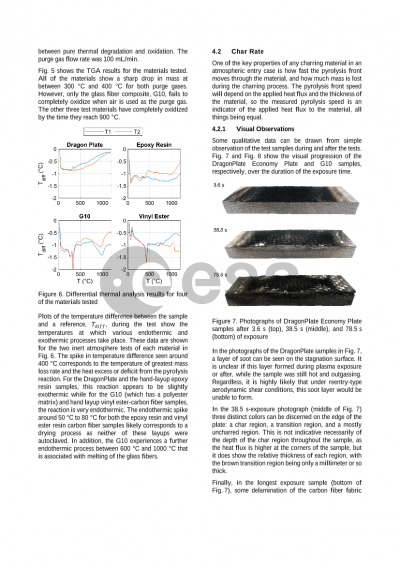
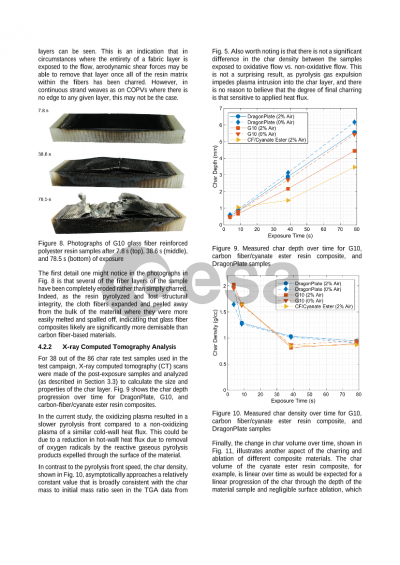
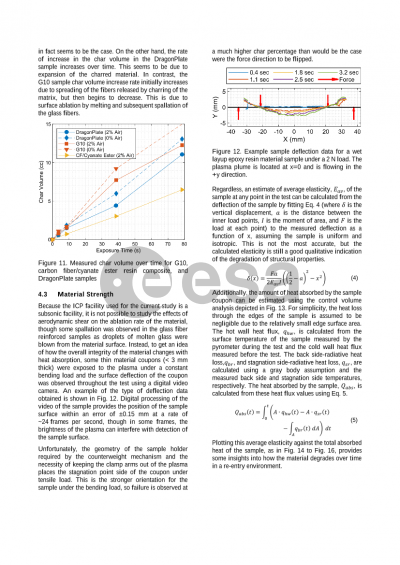

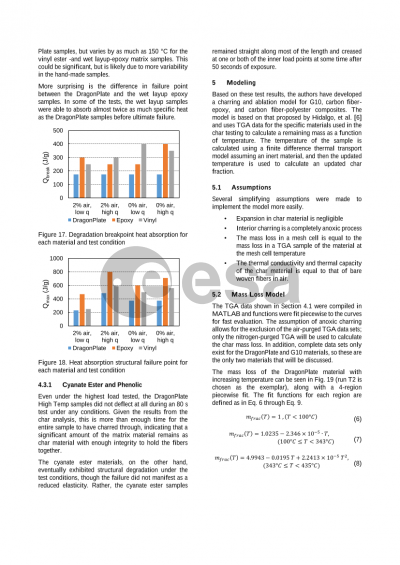
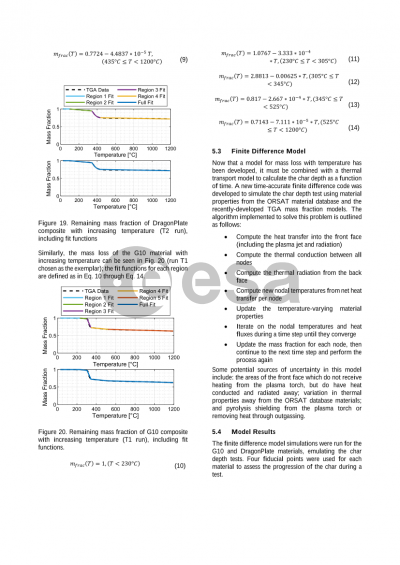
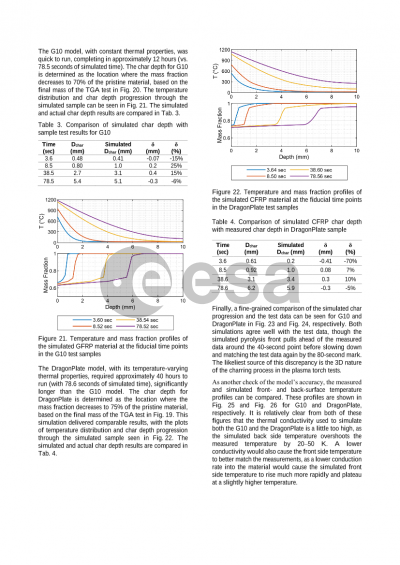

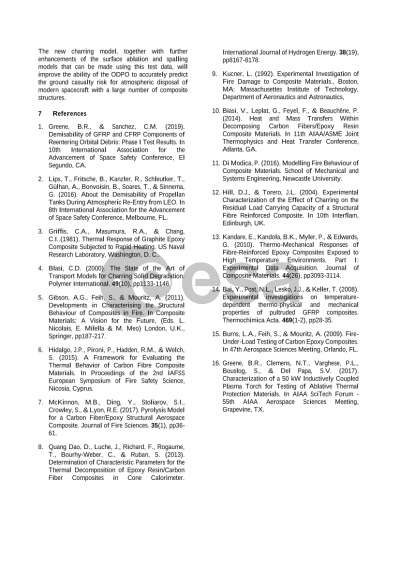