Document details
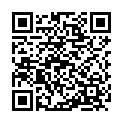
Abstract
The NASA-ISRO Synthetic Aperture Radar (NISAR) space mission is a collaboration between NASA and the Indian Space Research Organization (ISRO). Work is underway on the NISAR Earth-orbiting spacecraft and its SAR science payload, for a launch in the early 2020s to a polar orbit of about 750 km altitude. The mission will provide spatial and temporal measurements of land surface changes having high societal impact, such as changes in the ice sheets, land vegetation, and land motion (e.g. earthquakes or landslides).
Many of the L-band SAR electronics boxes are mounted on the exterior of the structure due to lack of volume in the instrument structure and also for thermal control. Depending on the data acquisition mode, the tops of either of two identical sets of boxes will be facing into the velocity direction, where they will be exposed to near-head-on impacts by space debris at speeds of about 15 km/s.
The tops of the boxes serve as radiator surfaces. These single-wall box lids function well as radiators, but are not very efficient debris shields. Unfortunately, a double-wall debris shield would impede the transport of heat out of the boxes.
The impact risk was estimated using NASA’s ORDEM3 debris model and Bumper impact analysis tool. Evaluation of the initial design showed a risk that was unacceptably high, so additional mass was allocated to increase the box lid thicknesses. If all of the boxes had equal importance and equal exposure to the debris environment, the lids should all be given the same thickness. However, each type of box has a different role in instrument functionality and survival, and these dependencies were captured in a reliability model. The model was used to optimize a distribution of shield mass among the boxes: total mass was minimized while maintaining a threshold of functionality and survival probability that was acceptable to the project. This paper describes the design process.
Preview
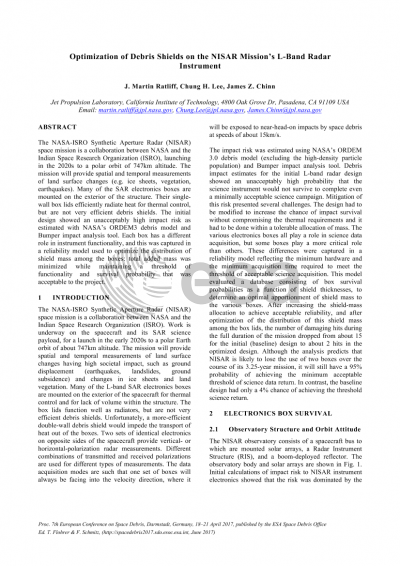



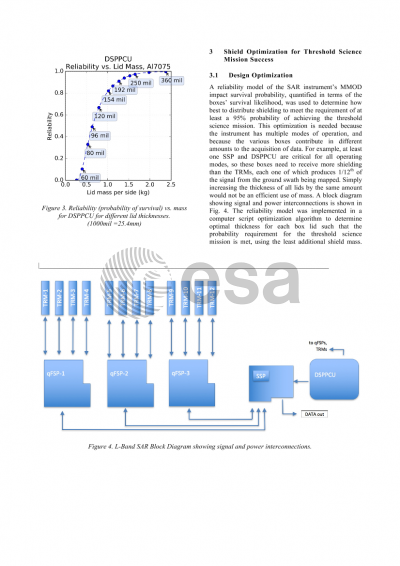
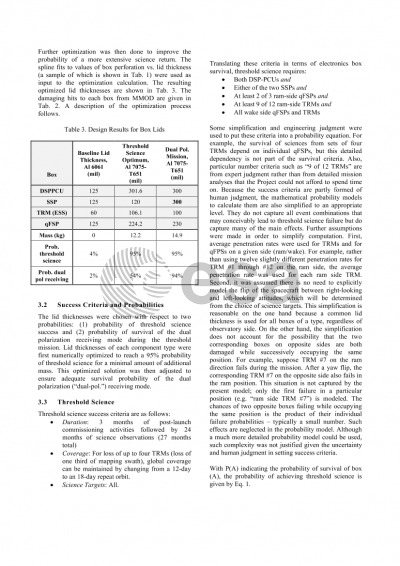
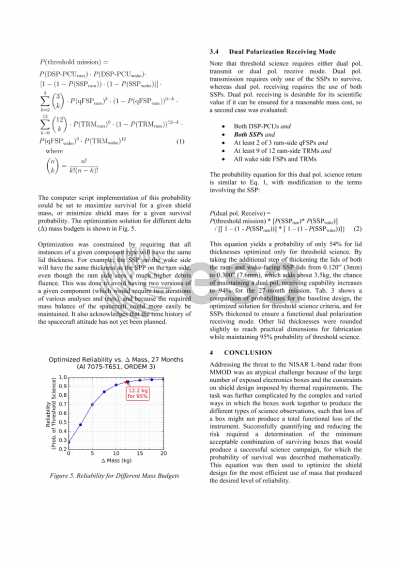
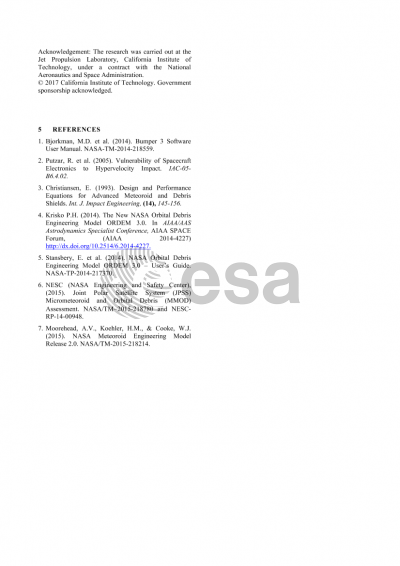