Document details
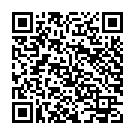
Abstract
Currently about 26,000 objects larger than 5 cm are tracked while orbiting near the Earth: most of this space debris is concentrated in the most useful Earth orbits, in particular 79% are orbiting in LEO. In order to suppress collisions between existing space debris, removal is the only solution: NASA and ESA agree on the urgent need to remove 5-10 strategically chosen debris every year. One of the most promising technologies for space debris removal is the use of throw-nets to capture debris, followed by one or multiple deorbitation burns during which the debris is pulled with a tether.
Over the recent years we have been studying technologies for Active Debris Removal aimed at maturing net-capturing. In particular, this paper will detail the design of a net ejector for capturing space debris. An engineering model, to be used in a full scale ground experiment, will be then manufactured, based on this design, to validate the system in a ground experiment. In fact the concept has already been validated at small scale on-board zero-G parabolic flights. We have also been developing a detailed high fidelity dynamics simulator.
The result is the design of a net ejector – developed on the base of the experience matured thanks to the parabolic flight experiments –, suitable for being installed in the chaser, based on one of the candidate platforms selected by ESA for a real Active Debris Removal mission. The ejector design is based on a cool gas generator, providing the compressed gas to eject four bullets attached to the net, folded inside a container. Two ejectors shall be accommodated inside the chaser, in order to ensure redundancy in case of failure. The design has been supported by high fidelity dynamics simulations and validated by environmental tests in a thermal vacuum chamber.
Preview

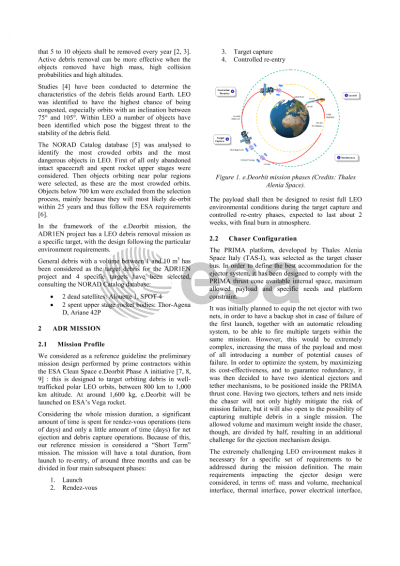
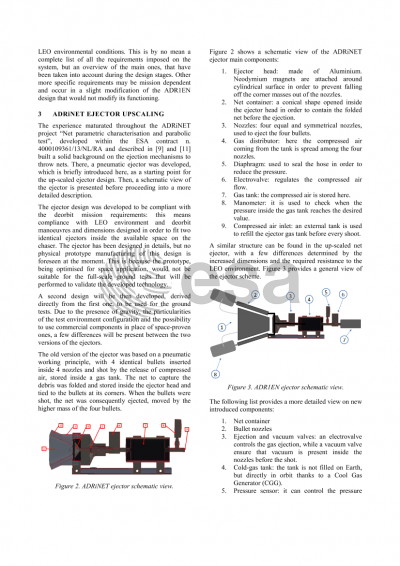

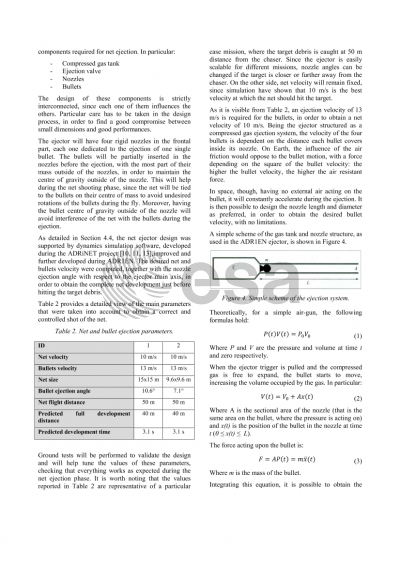



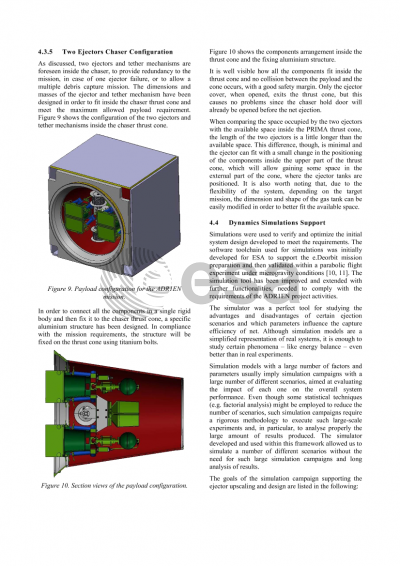

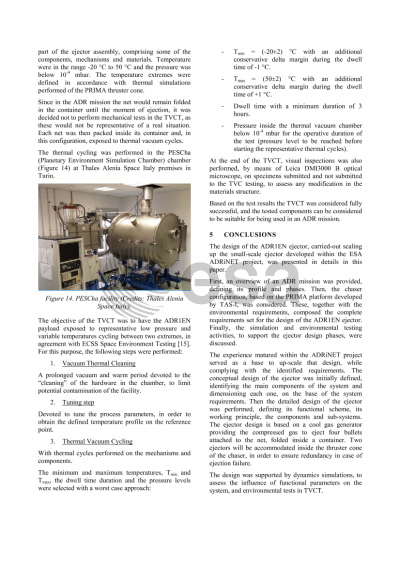
