Document details
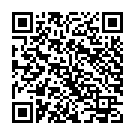
Abstract
Solid rocket motor propellant contains aluminum particles to stabilize its combustion. These aluminum particles bind to the oxidant, and then ejected as aluminum oxide particles. The size of these particles is a few micrometers. At the final phase of the combustion, on the other hand, the solid rocket motor ejects larger aluminum oxide debris. This debris is called solid rocket motor slag. As shown in the debris environment model, MASTER-8, most of the slag ranges from sub-millimeters to a few millimeters in size. The slag accounts for much of the debris in orbit due to past rockets, and the possibility of impact with a spacecraft is great. The slags collected after the solid rocket motor ground combustion experiment had various porosities, with porosities of some slags reaching over 90%. The purpose of this study is to investigate the effect of porosity within projectiles on the impact crater shape.
Hypervelocity impact tests were performed at Kyushu Institute of Technology using collected slags from the ground combustion experiment of a small solid rocket motor conducted by JAXA. These slags were too brittle to accelerate as a projectile with the two-stage light gas gun. Therefore, the authors selected the revere impact method. An aluminum-alloy cylinder was set in the launch tube as a target. The target was accelerated and passed through guide rails to stabilize its impact orientation. The slag was put into the guide rails. After the impact point, the gap of the guide rails was tapered. Therefore, the target decelerated gently after impacting the slag. At the exit of the rail section, stacked polystyrene sheets were installed to collect the target with the crater.
The numerical simulation was performed using the hydrocode, ANSYS Autodyn, with a 3D Lagrange method. The slag was modeled as a spherical shell of aluminum oxide. The crater shape closely resembled the experimental result. However, the elevation at the center of the crater was lower than that in the experimental result. Consequently, the slag model was modified to incorporate two voids by introducing a wall within the shell. In the simulation result of the slag with a wall parallel to the impact axis, the damage along the impact axis was more extensive due to the wall’s penetration. The model with a perpendicular wall was also analyzed. When half of the slag penetrated the target, the crater shape was nearly identical to that of the shell model. Subsequently, however, the impact of the wall flattened the elevation, making the top of the elevation resemble the experimental result. The internal structure of the slag was found to influence the crater shape.
To simulate the complex structure inside the slag, the slag was initially modeled using 3D-CAD. The CAD model was then imported into ANSYS LS-PrePost, where a mesh structure was generated. This model was subsequently imported into Autodyn to produce the SPH model. The simulated crater shape was found to be in good agreement with the experimental result.
Preview
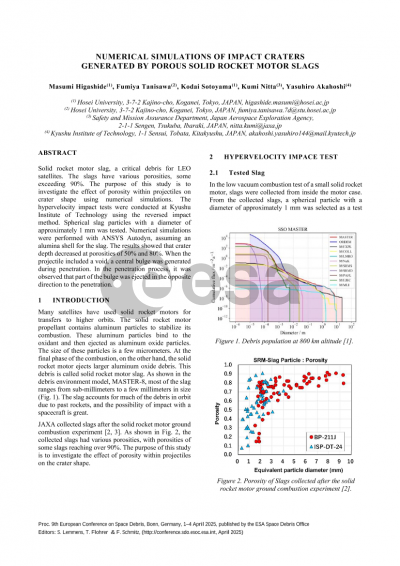
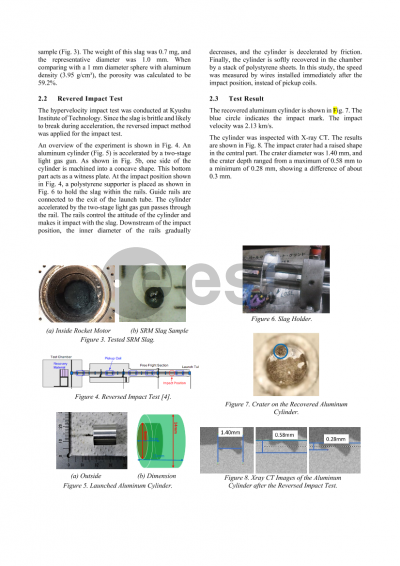
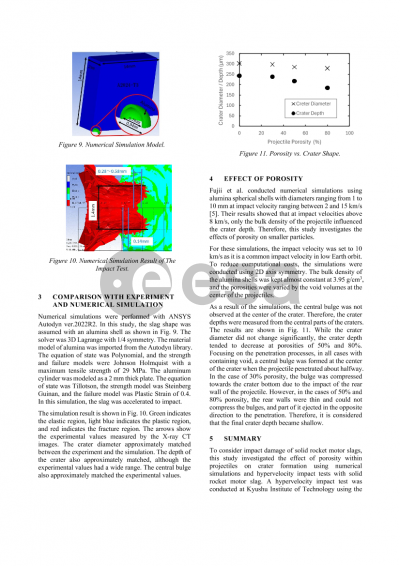
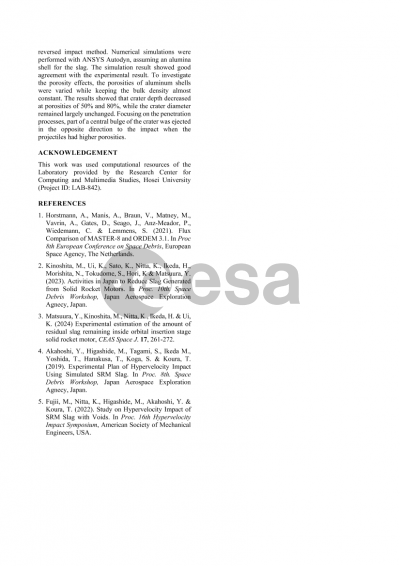