Document details
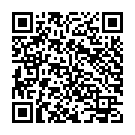
Abstract
Pressurized tanks onboard spacecraft and upper stages may rupture when impacted by a sufficiently energetic micrometeoroid or space debris particle. So-generated tank fragments hit the surrounding vehicle with considerable kinetic energy, causing further destruction. As a consequence, a significant number of particles is released into the space debris environment, contributing to the particle impact threat for future missions.
The ESA study “Impact Safe Tank Pressure Level” aims to add to the already existing database of impact tests on unshielded metallic tanks made of titanium by means of both impact experiments and numerical simulations. The approach of the study is to verify the numerical simulations through available impact test data, use the so-verified models to predict critical impact conditions, confirm the predictions by experiments on sub-scale tanks, and finally perform full-scale simulations on realistic tank sizes. The major challenges for numerical simulations are the high strain rate impact loading of the tank wall material and large tank volumes (ca. 0.6 m diameter) in combination with comparatively thin tank walls (ca. 1 mm). On the experimental side, the possible amount of impact tests is strongly limited by comparatively high manufacturing costs for realistic tank specimen.
During the study it became evident that not enough material data was available for the numerical simulations. Especially material data at high strain rates was missing. Therefore, an extensive material characterization of titan grade 2 was performed. The numerical model was updated using this newly generated data.
During the study, hypervelocity impact tests were performed on eight tank samples. Two different wall thicknesses (0.6 and 0.9 mm) were investigated experimentally. Prior testing, one specimen per wall thickness was subjected to static burst testing. In the impact tests, the rupture limit for both wall thicknesses could be established experimentally. In total, the study generated robust data for modeling the rupture threshold of metallic titanium tanks.
The contribution introduces the study, the challenges for impact experiments and numerical simulations, presents the concept behind the numerical simulations and outlines the material characterization performed to tune the numerical material models. The focus of the contribution is on the results of the hypervelocity impact experiments performed.
Preview
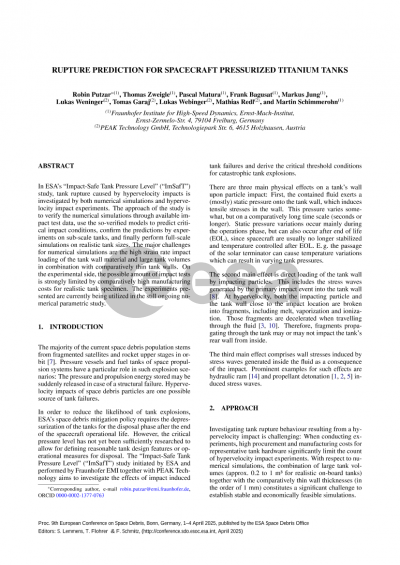
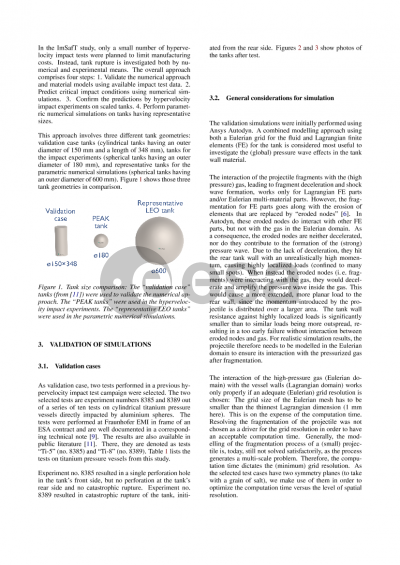
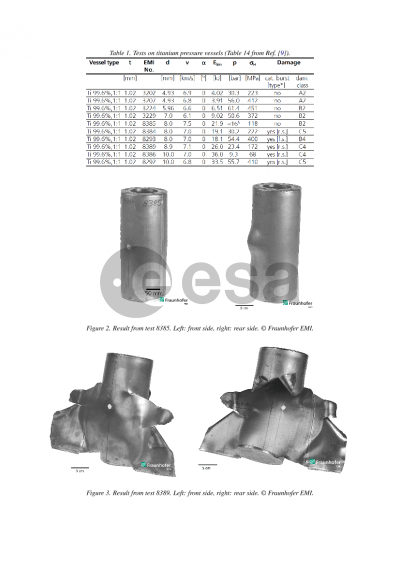
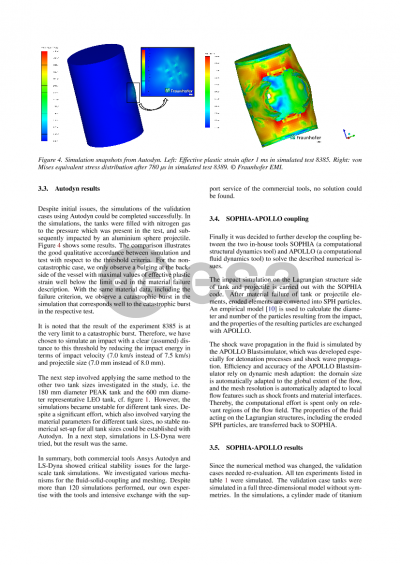
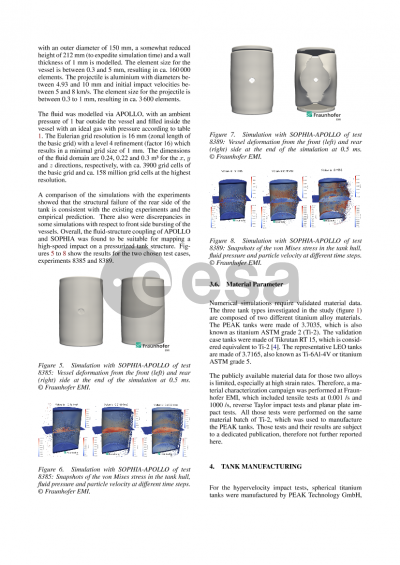
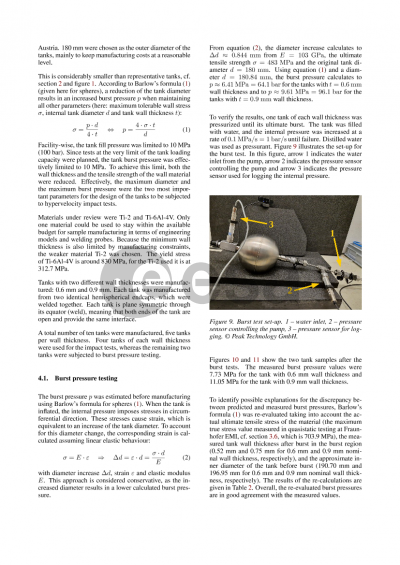
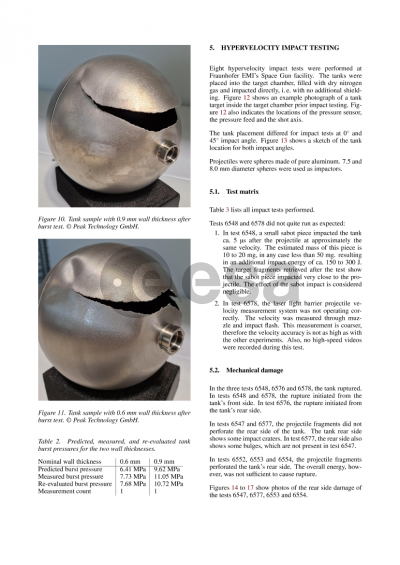
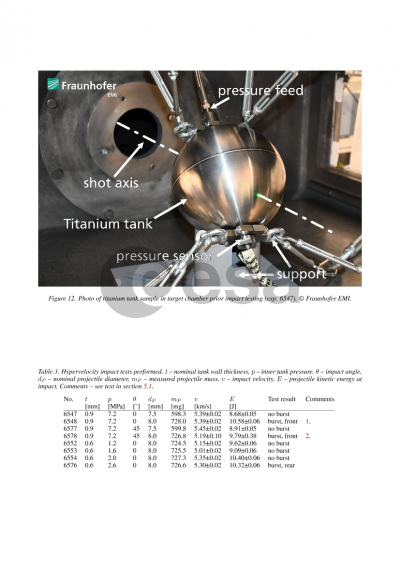
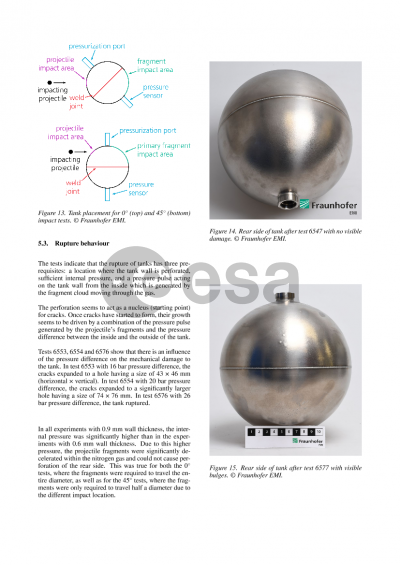
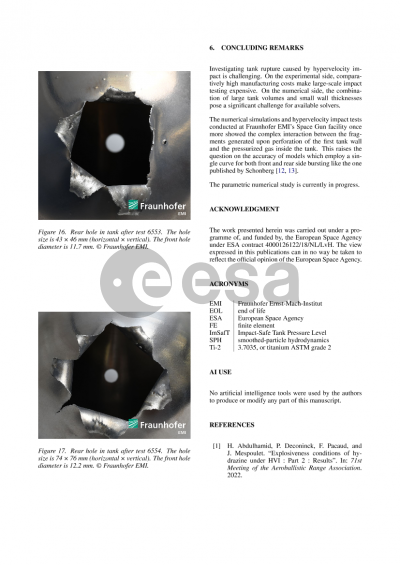
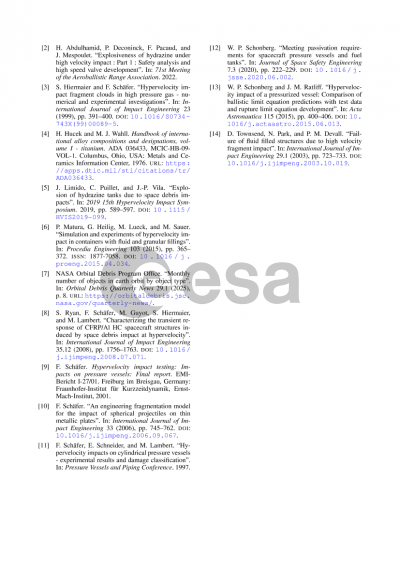