Document details
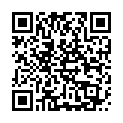
Abstract
The exponential growth of artificial satellites has heightened the urgency for sustainable and safe deorbiting strategies to mitigate the accumulation of space debris. Design-for-Demise (D4D) principles emphasize the development of satellite components that disintegrate during uncontrolled atmospheric reentry, minimizing risks to life and property. This joint study combines advancements in hybrid demisable joints and physical vapor deposition (PVD)-based coatings, presenting complementary approaches to enhancing the disintegration of satellite structures.
The German Aerospace Center (DLR) Institute of Structures and Design has extensive experience in the development of hybrid, additively manufactured demisable joints for thin plates within the DLR TEMIS-DEBRIS project, based on the reference case of the EU:CROPIS satellite. These joints are engineered to initiate high-altitude breakup, providing critical satellite components extended exposure to high-temperature plasma flows, which facilitates their complete demise. Benefiting from the advanced manufacturing techniques, the study integrates 3D-printed materials, such as PEI and CF-PEEK, with a passive ejection mechanism using shape memory alloy (SMA) and compression springs. Extensive Finite Element Analyses (FEA) optimize the design and material selection, ensuring the joints endure launch loads while enabling predictable disintegration during re-entry. Validation through oven tests and fragmentation simulations using the ESA DRAMA tool underscores the feasibility of these innovative joints for small and also for large satellite applications.
Complementing this structural approach, at the DLR Institute of Material Research the use of PVD-based coatings aims to enhance the demisability of high-melting-point metallic components, such as those made from V4A stainless steel. By applying catalytic coatings via magnetron sputter deposition, this study focuses on increasing heat flux to substrates while reducing radiative heat loss. A dual-layer system, comprising Al, Si, Cr, or NiAl coatings with a thin copper layer, promotes the rapid formation of thermally grown oxide scales during reentry. Experimental validation through laboratory tests at temperatures up to 1300 °C and arc-heated wind tunnel simulations confirms the coatings' ability to induce predictable thermal failure. Advanced characterization techniques, including XRD, SEM, and EDS, provide insights into coating morphology, adhesion, and performance under extreme conditions.
Together, these innovations represent an approach towards a more sustainable satellite design, integrating structural and material solutions to ensure safe and efficient demise process.
Preview
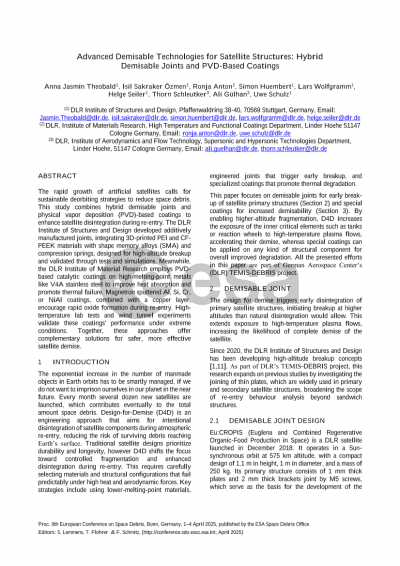
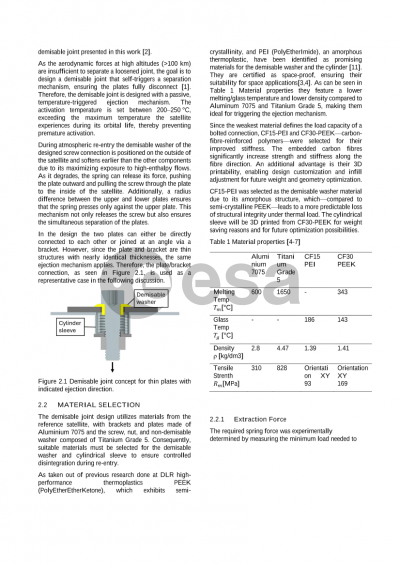
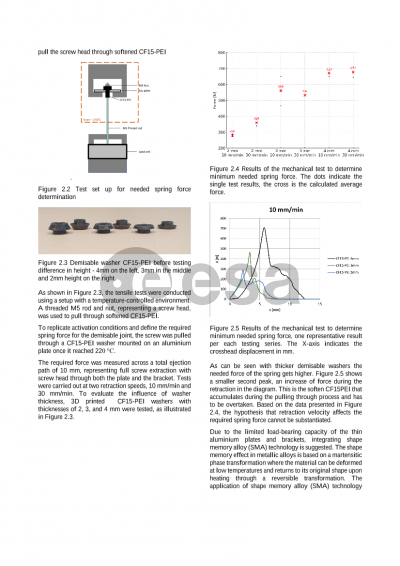
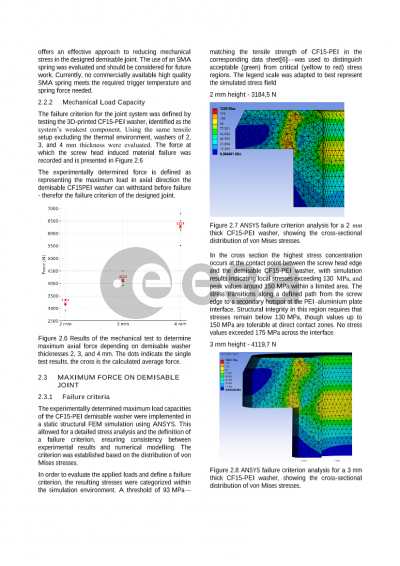
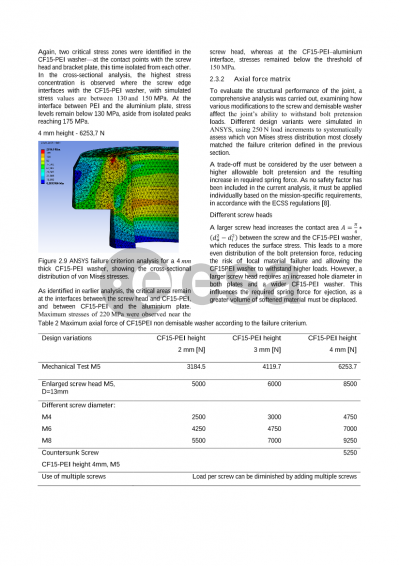
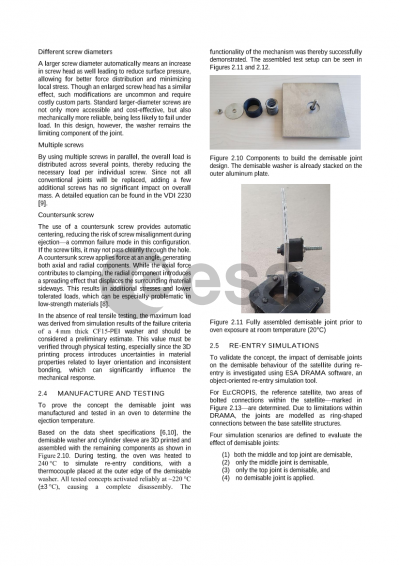
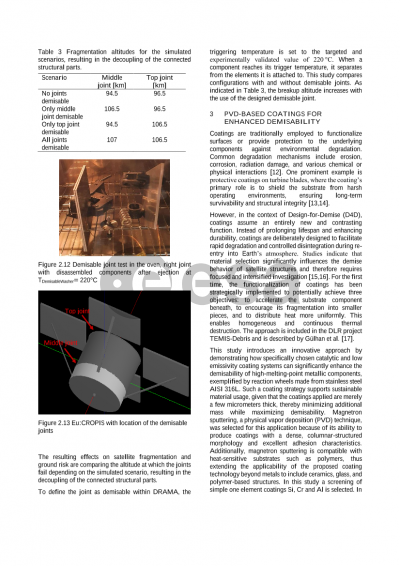
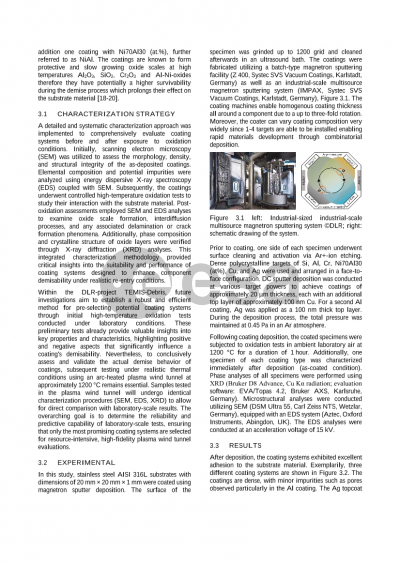
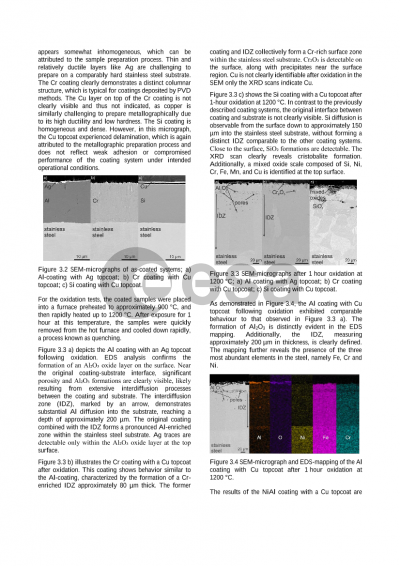
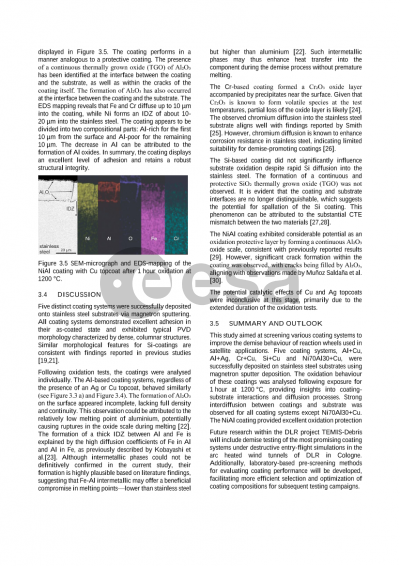
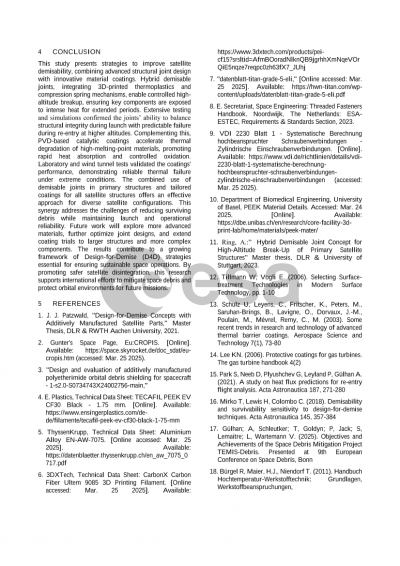
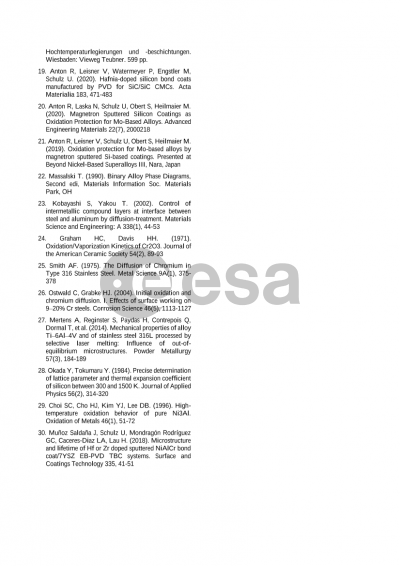