Document details

Abstract
The destructive impact of atomic oxygen (AO) on spacecraft within near-Earth altitudes has been extensively documented by the scientific community, beginning with early space shuttle missions [e.g. 1].
The high reactivity of AO, coupled with the exacerbated erosive potential due to the high velocities of spacecraft in low Earth orbit (LEO), can result in considerable erosion and mass loss. Materials used for structural support, thermal control, and coatings that contain organic polymers are particularly vulnerable to AO attack at high velocities, leading to erosion and surface roughening [2]. This can progressively impair the spacecraft's structural integrity and operational efficiency. In addition, material erosion and surface roughening due to AO can weaken spacecraft structures, potentially increasing the risk of debris generation under certain conditions. Thus, an in-depth understanding of how materials behave under space conditions is critical in anticipating the likelihood of fragmentation and other processes that contribute to the growing issue of space debris.
This study conducts long-duration experiments to assess the effects of AO on three types of thin polymer films: blank Kapton®, Kapton® coated with a thin Indium Tin Oxide (ITO) antistatic layer to mitigate onorbit plasma charging, and breadboard model (BBM) material consisting of a conductive grid sheet (copper etched on Kapton®). Additionally, these materials were perforated to simulate a micrometeoroid orbital
debris impacts to further characterize material degradation when the underlying material with ITO coating has been exposed to AO. Exposure testing of sample materials to an 8 km/s oxygen atom beam was
conducted according to ASTM-E2089-15A using the FAST source at the Physical Sciences Inc (PSI). Effective peak atomic oxygen fluence during the run will correspond to ~ 18 months of LEO exposure (2 x 10^21
atoms/cm^2).
Optical images of each material in its pristine and AO-exposed state, as well as defect count, surface roughness, and elemental compositional analysis measurements of each sample, were performed using
Keyence VHX-7000 optical microscope with laser-based elemental analysis attachment. In addition, mass loss measurements were performed by PSI after the AO-exposure test completion.
The following will provide an overview of AO in LEO, present details on the materials subject to AO testing and the experimental process, highlight the laboratories used for this study, summarize the results and
analysis completed, and lastly present recommendations based on this study to enhance spacecraft materials planned for long-duration exposure to AO.
[1] L. J. Leger. NASA TM-58246 (1982)
[2] R. Tennyson. Can. J. Phys. 69, 1190−1208 (1991)
Preview
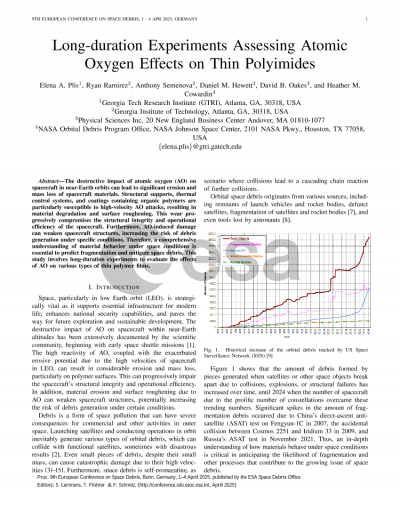
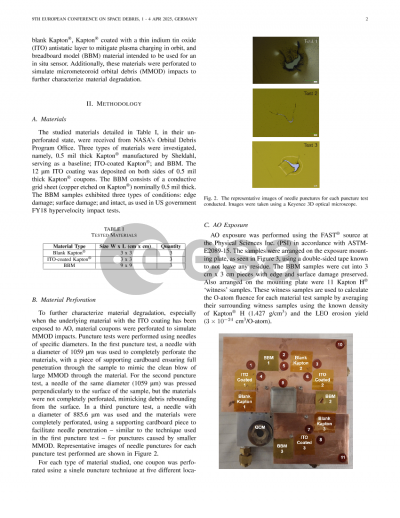
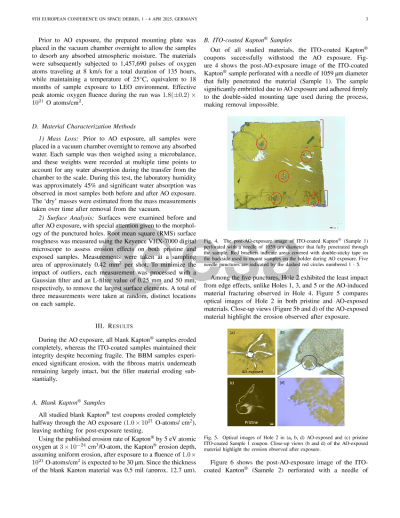
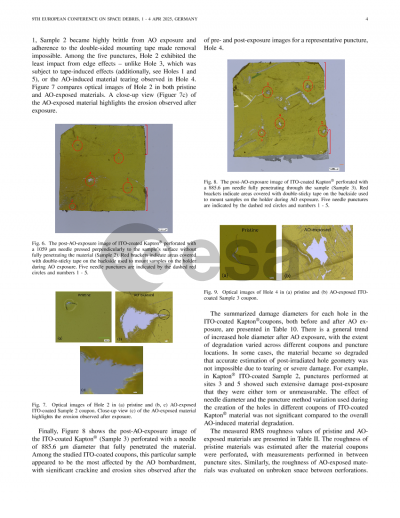
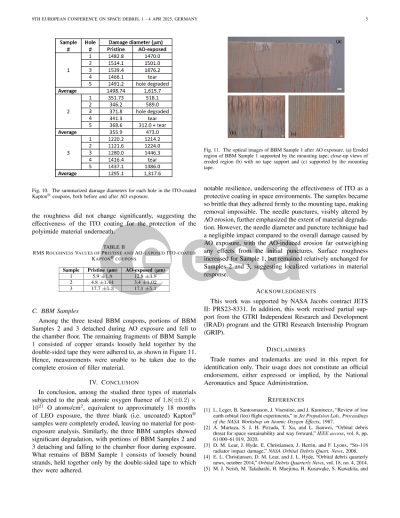
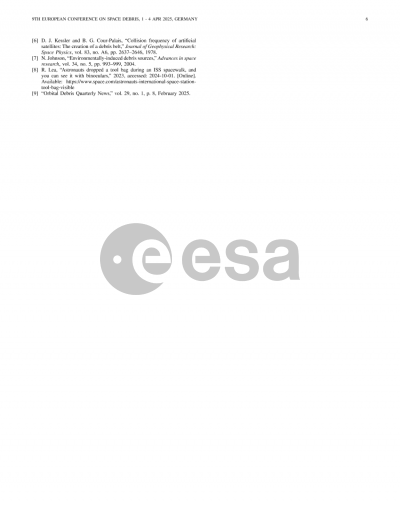